Le 20/07/2012
Essais Libres 1
Essais Libres 2
***
Le 21/07/2012
Essais Libres 3
Qualifications
***
Le 22/07/2012
Course
(67 Tours)
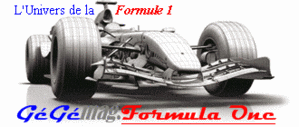
GéGémag.Formula Onel'Univers de la Formule1
Le châssis de la voiture, monocoque ou tubulaire, est la partie centrale de la voiture où tout est rattaché. Il comprend le pilote, donc il doit être capable d'absorber de gros chocs, mais ne peut peser que 35 kg ! Le châssis tubulaire, comme beaucoup de pièce dans une F1, est fait en fibre de carbone (85% de la voiture en est composé). Ce matériau d'abord développé par l'aérospatiale est 5 fois plus léger que l'acier et 2 fois plus résistant. Il est idéal pour la conception de Formule 1. Le châssis doit donc pouvoir résister aux forces très importantes produites par les vitesses élevées, les secousses et la charge aérodynamique imposés à la voiture. La procédure pour fabriquer des pièces en carbone est la suivante : Le baquet est d'abord conçu sur un logiciel de CAO (Conception Assistée par Ordinateur) puis une machine contrôlée par ordinateur découpe des morceaux d'ureol pour en faire un moule (procédé au laser : ces moules sont fait en quelques minutes). L'ureol n'est pas très différent du bois, mais c'est un matériel synthétique qui n'absorbe pas l'eau. Il est également moins granuleux et ne se transforme pas avec la température, ainsi des modèles très précis peuvent être faits. Ces modèles de châssis sont alors couverts de fibres de carbone pour créer le moule final à partir duquel le châssis sera conçu. La fibre de carbone est entreposée en rouleaux et doit être réfrigérée jusqu'à son utilisation. On applique ensuite de la résine et un durcisseur sur les parties à agencer afin de former un tout. Une fois le moule obtenu, il est poli dans toute sa partie intérieure puis enduit de lubrifiant pour faciliter le démoulage du baquet final. Le moule est soigneusement rempli de couches de fibres de carbone. Les fibres de carbone se présentent comme n'importe quels tissus mais ils peuvent être chauffées, leur procurant alors une incroyable solidité. La façon dont ces fibres sont disposées est très importante car les fibres jouent un rôle primordial dans l'absorption des efforts et des forces subies par la monoplace vers d'autres parties du châssis. La fibre est travaillée pour s'adapter exactement au moule du châssis. Le nombre de couches souhaité atteint, le moule est alors mis dans une machine à vide (sac hermétiquement fermé et pressurisé) pour littéralement sucer la couche de carbone afin de l'adapter le plus possible au moule. Le nombre de couche nécessaire diffère d'une zone à une autre, plus les pièces sont soumises à des contraintes importantes, plus elle aura de couches. Le nombre moyen est d'environ douze couches. Pour renforcer la rigidité, une couche en nid d'abeille d'aluminium est positionnée au milieu des couches de carbone. Une fois le nombre correct de couches appliquées, le moule est mis dans un four autoclave où il est chauffé et pressurisé. Le four autoclave a la particularité de pouvoir faire un vide partiel et de pouvoir changer l'atmosphère qui y règne en la remplaçant par d'autres gaz dont les atomes se fixent sur les pièces. Cela peut ce produire juste sur la surface des pièces, ou même pénétrer la pièce et ajouter de nouvelles caractéristiques aux matériaux. Les températures élevées libèrent la résine des fibres et la haute pression (plus de 100 psi) scotche les couches entre elles. Tout au long de ce processus, les fibres durcissent et se solidifient pour un résultat final atteint au bout de deux heures et demi. Quand tout est terminé, on ponce et on peint les pièces aux couleurs de l'équipe. Les parties internes tels que les pédales et le tableau de bord sont collés directement dans le baquet grâce à de la résine d'époxy. Le réservoir est situé juste derrière le siège du pilote. Il est constitué à partir de deux couches en caoutchouc, du butadiène de nitrate, avec une couche extérieure en kevlar renforcé pour empêcher toutes cassures. Les dimensions du réservoir sont très précises afin qu'il soit parfaitement intégré au châssis et qu'il ne puisse bouger sous les G élevés encaissés par la monoplace. Les durites reliant le réservoir au moteur sont facilement déconnectables de façon à ce que lorsque le moteur se sépare du châssis lors de graves accidents, le carburant soit arrêté automatiquement. Chaque pièce en carbone doit être testée avant de l'utiliser afin de prévenir tout défaut, car si une pièce lâche à 350 km/h, cela peut devenir très dangereux pour le pilote.
Un atelier de ce genre peut coûter jusqu'à $50 millions car en plus d'y fabriquer toutes les pièces en carbone pour une monoplace, on y fabrique aussi toutes les pièces réduites pour les tests en soufflerie. Inutile de dire que seules les équipes fortunées peuvent se permettre un tel laboratoire. Châssis complet avec la suspension avant. Le reste du châssis est formé par le boulonnage du moteur, de la boîte de vitesses et du différentiel à ce même châssis.
La carrosserie comprend tout ce qui recouvre les pièces de la voiture. Elle inclut le revêtement du châssis, les ailerons, les pontons et le capot qui comprend la prise d'air au-dessus du pilote. Le tout est fabriqué en fibre de carbone de la façon indiquée plus haut. C'est probablement la partie de la voiture la plus étudiée pour l'aérodynamisme car c'est elle en grande partie qui fera écouler l'air autour de la voiture. Chaque partie de la carrosserie a son rôle : les ailerons provoquent de l'appui (freinent la voiture), les pontons et la bouche d'aération font entrer l'air pour refroidir le moteur tout en résistant le moins possible au passage de l'air, et le reste est étudié pour faire glisser l'air tout autour de la voiture.
Lors dun accident aussi violent et improbable soit til, le pilote doit être protégé de lenvironnement extérieur par la coque de survie. Toutes les monoplaces sont constituées autour de la cellule de survie qui protége le pilote. Outre lhabitacle cette cellule comprend larceau de sécurité et le réservoir. A notre époque où la sécurité est devenue primordiale cette cellule rigide doit résister à tous les chocs et ce même si le reste de la voiture est détruit. Mais ne vous y trompez pas, la F1 ne doit surtout pas être complètement rigide est indestructible, au contraire elle doit être étudiée de façon à être détruite sans que le pilote soit blessé. Cette structure absorbe lénergie au fur et à mesure de la destruction de la monoplace.
Le meilleur règlement possible :
Cest la direction de la FIA et le groupe de travail Technique qui en se réunissant régulièrement définissent les limites de la survie de la voiture. Ils sont aussi conseillés par les médecins de la FIA pour ne pas dépasser les décélérations maximales quun corps humain peut supporter. Les règles deviennent de plus en plus stricte. On ne joue pas avec la sécurité ! Lévolution est fulgurante il ya à peine 20 ans les monoplaces navaient que des structures rudimentaires de résistance aux chocs. A lheure actuelle les monoplaces apportent une protection frontale, latérale et arrière au pilote.
Lévolution des matériaux :
La F1 devient de plus en plus sophistiquée avec de nouveaux matériaux bien meilleur que par le passé. La fibre de carbone a permis une nette amélioration de la sécurité. Elle est composée de matériaux de différentes natures qui réagissent aux chocs de façon différents. Les métaux peuvent sous de violents choc se froisser et se déformer brutalement par contre les fibres de carbone sarrachent progressivement car elles sont incorporées dans de la résine. Lors dun choc violent ces fibres absorbent lénergie en sécrasant. Les couches de carbone se séparent, ou les fibres sarrachent de la résine et ainsi absorbent beaucoup dénergie.
-Etudier un bon châssis :
La réalisation du châssis :
Létude de conception du châssis est lancé au moins un an avant sa première course. Les objectifs sont définis comme par exemple la distribution des masses, la capacité des réservoirs ou encore la résistance à la torsion. Le but est dobtenir une coque fine et mince mais aussi résistante, efficace et légère. Le compromis est dur à trouver !
Résistance aux chocs :
Lévaluation première de la résistance est étudié sur ordinateur. Cest lanalyste des efforts qui est chargé de définir un réseau de points à la surface de la coque via lordinateur, puis de leur appliquer une charge et détudier la réaction du maillage. Cette étude est très complexe et il faut bien un mois pour définir les couches stratifiées, quil faudra incorporés lors de la fabrication.
Etude de l'encaissement d'un choc
Construire le châssis :
La construction dun châssis en fibre de carbone nécessite de très bon technicien car elle est très complexe. Ainsi certaines zones nécessitent plus de 30 couches pour avoir la résistance nécessaire. Létude par ordinateur permet de concevoir un plan précis de lorientation et du nombre de chaque couche. Puis un plan sous la forme dune représentation imagée de chaque couche (un peu comme un patron de tailleur) est transmisse au département des composants, avec parfois plus de 100 pages !
Ce nest quà lautomne que les écuries commencent à travailler réellement sur les châssis puis les tests décrasement commencent en novembre. Au début les tests décrasement sont réalisés sur des petites pièces isolées comme le nez ou larceau de sécurité.
La dernière étape le crash test :
Toutes les coques (et pas seulement la première de chaque évolution) doivent résister à un essai de crash-test. C'est-à-dire quelles doivent en ressortir intacte et réutilisable. « Nous voulons passer, mais avec des marges très faible » nous dévoile Gary Savage, directeur technique délégué de Honda F1. « Nous faisons toute une série dessais pour être sûrs à 95% de réussir. Un des châssis subit toute la batterie des crash-tests et devient la référence pour les autres. La FIA exige quil en sorte intact et il nest pas dans notre intérêt de détruire un châssis à $100.000. » Et donc les châssis réussissent souvent au premier examen. Les châssis nayant pas passé avec succès ce test existent et même parmi les grandes écuries. On se souvient de la McLaren MP4-18A (2003) qui a échoué au crash test, malgré les efforts des ingénieurs pour la rendre plus solide.